PROPOS vormt de ruggengraat voor productiebedrijven die streven naar snelle, tijdige en moeiteloze productie. Onze bedrijfsbrede oplossing voorziet in diverse tools waarmee alle medewerkers gezamenlijk werken aan het nakomen van klantbeloften. Op de werkvloer worden afdelingen of teams aangestuurd, gemonitord en geoptimaliseerd met behulp van PROPOS-schermen die real-time de uitvoering van werkzaamheden weergeven. Via het dashboard kunnen productieleiders in één oogopslag zien waar aandacht nodig is en waar alles soepel verloopt. Bovendien maken personen belast met procesverbetering op langere termijn gebruik van PROPOS-analyses om te bepalen welke delen van de productie prioriteit verdienen voor verbetertrajecten. In deze analyse duiken we dieper in op een van deze analyses die PROPOS genereert met slechts één druk op de knop: de Work In Process (WIP)-analyse.
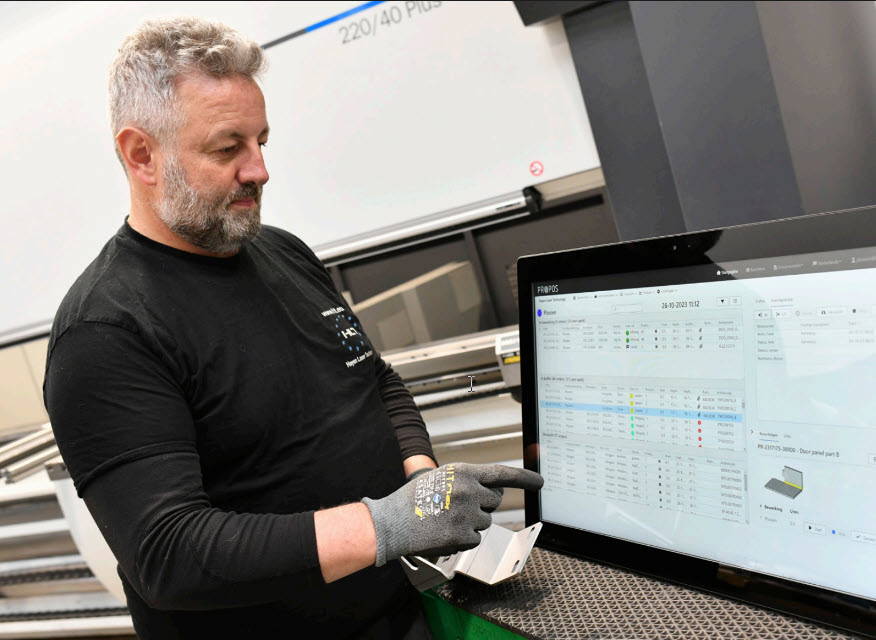
“Productieleiders kunnen via het dashboard in één oogopslag zien welke onderdelen van productie aandacht nodig hebben en waar alles goed gaat.”
Om deze analyse toe te lichten, nemen we mijn autorit over de A15 als voorbeeld.
Op 15 april had ik om 12.30 uur een afspraak in Moerdijk. De routeplanner voorspelde een reistijd van 1 uur en 50 minuten. Wetende dat tegenslagen altijd mogelijk zijn (en ik onderweg nog wilde lunchen), plande ik bijna 2 ½ uur in voor deze reis, met een marge van ruim 30 minuten. Helaas/onverwacht vond midden op de ochtend een ongeluk plaats bij Hardinxveld, ongeveer een kilometer voor mij. Dit ongeluk veroorzaakte een volledige blokkade van de snelweg. Terwijl de tijd verstreek en mijn aankomsttijd van 12.30 uur naderde, stond ik nog steeds stil op de snelweg. Ik moest onze klant op de hoogte brengen van mijn verlate aankomst. Hoeveel later? Dat was onzeker, hopelijk tegen 13 uur of 13.30 uur. Alle auto’s stonden stil, soms bewogen we stapvoets. Een half uur later moest ik opnieuw bellen om aan te geven dat 13 uur ook niet haalbaar was. Zou het dan 14 uur worden? Uiteindelijk bereikte ik Moerdijk rond 14.45 uur, een scenario dat velen maar al te bekend voorkomt.
Net zoals op de snelweg ontstaan er in productieprocessen vaak files. Orders (materialen) verplaatsen zich over de werkvloer van bewerking naar bewerking, waar ze telkens stilstaan omdat ze niet direct kunnen worden verwerkt bij aankomst. Als er te veel werk zich opstapelt bij een bewerking, ontstaat dezelfde vertraging als die ik op de snelweg ervoer. Orders blijven veel langer stil liggen dan verwacht, wat het voorspellen van hun voltooiing bemoeilijkt. Aan de andere kant, wanneer orders vlot doorstromen, zijn doorlooptijden en leveringsbetrouwbaarheid voorspelbaar. Net zoals ik mijn aankomsttijd kon voorspellen wanneer ik ongestoord op de snelweg reed, kunnen we ook voorspellen wanneer orders gereed zullen zijn als ze vlot door de productie stromen. Dit is precies wat we nastreven. Dit vereist het voorkomen van files op de werkvloer en het snel detecteren ervan wanneer ze toch onverwachts ontstaan, bijvoorbeeld door machinestoringen of een tekort aan personeel.
Zoals je misschien al weet is PROPOS gebaseerd op onder andere de principes van Quick Response Manufacturing (QRM), ontwikkeld in de VS door professor Rajan Suri. In een van zijn boeken legt hij dit principe uit en illustreert hij wat te veel werk doet met wachttijden en leveringsbetrouwbaarheid.
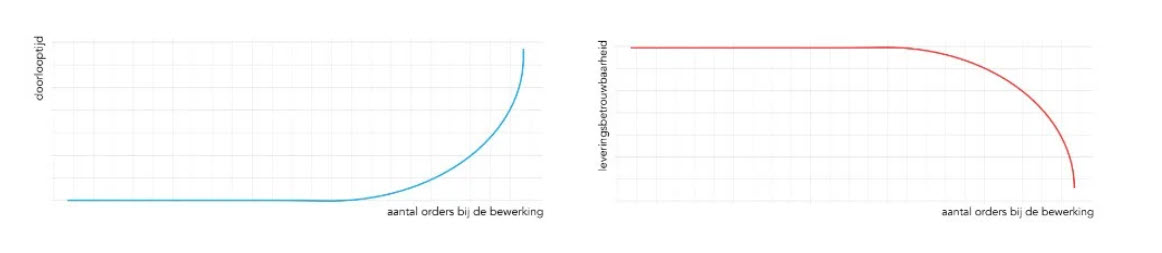
PROPOS biedt real-time ondersteuning bij het voorkomen en signaleren van dit soort filevorming. Dit zal ik echter in een andere post verder uitdiepen. Met PROPOS kun je echter ook een voorbije periode analyseren om te zien waar filevorming is ontstaan, zodat je passende maatregelen voor de toekomst kunt nemen. Een van de hulpmiddelen hiervoor is de WIP-grafiek, de Work In Process grafiek. Deze grafiek spoort werk op dat eigenlijk helemaal niet op de werkvloer hoeft te liggen en dus voor onnodige drukte zorgt. Ook zie je welke afdelingen (regelmatig) bottlenecks worden. Met die informatie kun je het onderhanden werk verminderen en samen met je medewerkers bekijken hoe je kunt zorgen dat orders sneller kunnen worden gestart als ze een afdeling bereiken.
Hoe werkt deze grafiek? Je bekijkt deze bijvoorbeeld per afdeling. Op de y-as staat het aantal uren werk dat zich in de afdeling bevindt. Op de x-as staat de tijd. Op het moment dat een order in een afdeling arriveert, stijgt de grafiek met het aantal werkuren voor die order in die afdeling. Op het moment dat een order de afdeling verlaat, daalt de grafiek met dat aantal uren. Bij het maken van deze grafiek zijn er drie belangrijke patronen om op te letten. Hieronder vind je drie voorbeelden van hoe een dergelijke grafiek eruit kan zien.
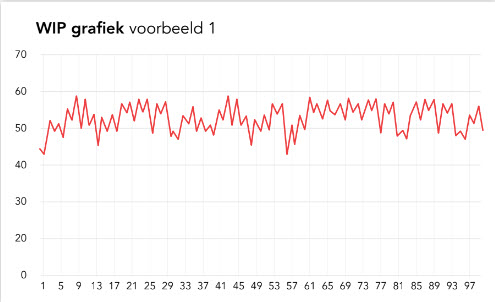
De eerste grafiek toont een afdeling die geen bottleneck is. De mate waarin werk binnenkomt is ongeveer gelijk aan de mate waarin er werk uitgaat. De oppervlakte onder de lijn is de hoeveelheid werk die continu op de werkvloer ligt. Dat ziet er met ruim 40 uren netjes uit.
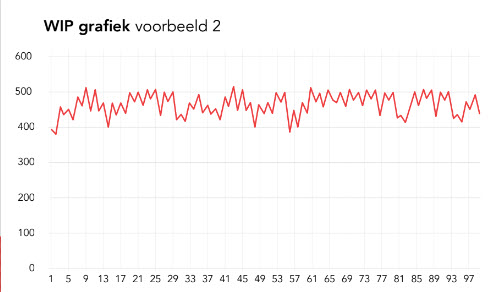
De tweede grafiek toont een afdeling die geen (verergerende) bottleneck vormt, maar waar wel continu heel veel werk ligt. Dit werk staat daar telkens lang te wachten. Je zou zo 300 uren werk uit deze afdeling kunnen halen zonder dat dat iets kost. Sterker nog, het maakt ruimte vrij, legt minder beslag op materialen, zorgt voor meer overzicht, meer flexibiliteit, kortere doorlooptijden en een hogere leveringsbetrouwbaarheid!
De derde grafiek toont een afdeling die in de betreffende periode een bottleneck was. Er komt op die momenten meer werk binnen dan dat de afdeling kan verwerken, waardoor de grafiek stijgt. Dat maakt de afdeling instabiel, wat zorgt voor lange en vooral onvoorspelbare doorlooptijden. Samen met je medewerkers kun je bekijken hoe dit kan worden opgelost. Misschien is crosstraining een oplossing, zodat de capaciteit snel kan worden verhoogd in geval van drukte. Misschien is steltijdreductie een goed idee, of het aanschaffen van een extra machine. Misschien is de voorcalculatie telkens te laag, waardoor meer tijd nodig is dan gedacht. Dit kan trouwens ook worden ontdekt via onze voor-/nacalculatie-analyse en onze leveringsbetrouwbaarheidanalyse, beide beschikbaar in PROPOS. Ook daarover zal ik meer informatie geven in een volgende post.

Met het bekijken van deze analyse en het nemen van maatregelen, hebben al vele bedrijven grote voordelen behaald. En wie met PROPOS werkt, haalt deze inzichten met een druk op de knop binnen. Wil je hier meer over weten? Neem dan gerust contact met ons op.